3D printing, also known as additive manufacturing, is a groundbreaking technology that has revolutionized the way we design and produce objects. From intricate prototypes to custom-made products, 3D printing offers a flexible and efficient way to bring ideas to life. But how exactly does this technology work? Here’s everything you need to know about the process, materials, and applications of 3D printing.
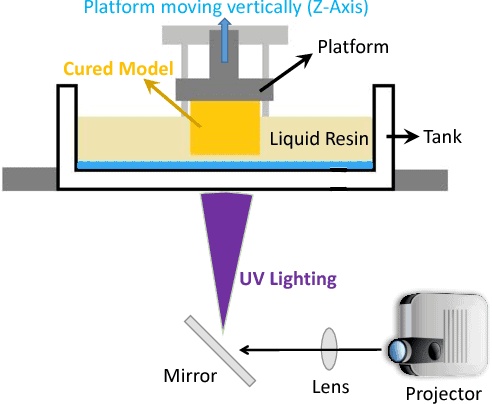
The Basics of 3D Printing
At its core, 3D printing is the process of creating a physical object from a digital model. Unlike traditional manufacturing methods that typically involve cutting or molding material, 3D printing builds objects layer by layer. This additive approach allows for greater design freedom and the ability to produce complex geometries that would be difficult or impossible with conventional techniques.
The process begins with a digital 3D model, which can be created using computer-aided design (CAD) software or scanned from an existing object. This model is then sliced into thin layers, which the 3D printer uses as a blueprint to construct the final object. Each layer is printed one at a time, gradually building up the object from the bottom to the top.
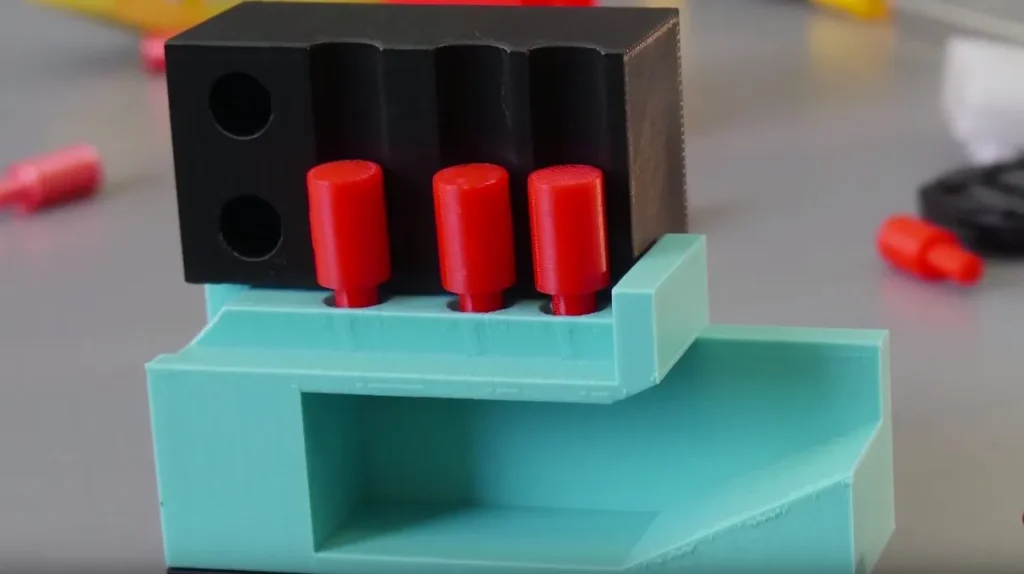
Types of 3D Printing Technologies
There are several different 3D printing technologies, each with its unique process and materials. The most common methods include:
- Fused Deposition Modeling (FDM): One of the most widely used 3D printing techniques, FDM involves melting and extruding thermoplastic filament through a heated nozzle. The printer lays down the material layer by layer, hardening it as it cools. FDM is popular for its simplicity and affordability, making it a go-to choice for hobbyists and prototyping.
- Stereolithography (SLA): SLA uses a laser to cure liquid resin into solid layers. The printer directs the laser onto the resin, hardening it where needed. SLA is known for producing high-resolution prints with smooth surface finishes, making it ideal for detailed models and prototypes.
- Selective Laser Sintering (SLS): SLS involves using a laser to fuse powdered material, such as nylon or metal, into solid layers. The laser selectively sinters the powder based on the digital model, and the un-sintered powder supports the object during printing. SLS is favored for its ability to produce strong, durable parts without the need for support structures.
- Digital Light Processing (DLP): Similar to SLA, DLP uses a digital light projector to cure resin. The entire layer is exposed to light at once, allowing for faster print times. DLP is known for its speed and accuracy, making it suitable for producing intricate designs.
- Binder Jetting: In this process, a liquid binder is selectively deposited onto a bed of powdered material, binding the particles together to form a solid object. Binder jetting is versatile and can use a wide range of materials, including metals, ceramics, and even sand.
- Metal 3D Printing: This category includes several techniques, such as Direct Metal Laser Sintering (DMLS) and Electron Beam Melting (EBM), which are used to create metal parts. These methods involve melting or sintering metal powder with a laser or electron beam to build objects layer by layer. Metal 3D printing is highly valued in industries like aerospace and automotive for producing complex, high-performance parts.
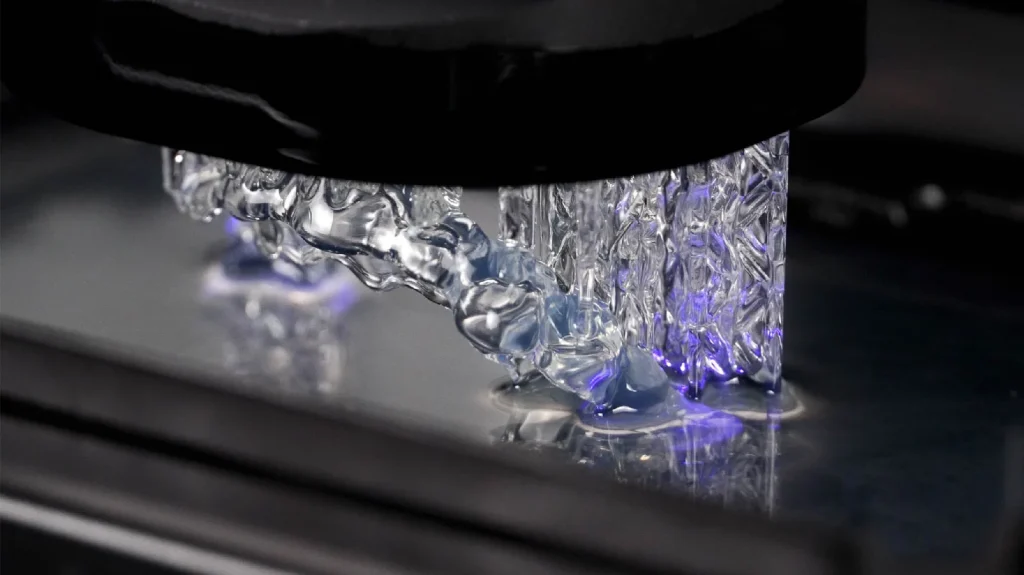
Materials Used in 3D Printing
The materials used in 3D printing vary depending on the technology and the desired properties of the final product. Some of the most common materials include:
- Plastics: Thermoplastics like PLA, ABS, and PETG are widely used in FDM printing for their ease of use and versatility. Resin materials are used in SLA and DLP printing, offering high detail and smooth finishes.
- Metals: Metal powders such as stainless steel, titanium, and aluminum are used in SLS, DMLS, and other metal 3D printing processes. These materials are prized for their strength, durability, and ability to withstand high temperatures.
- Ceramics: Ceramic materials can be printed using binder jetting and other specialized techniques. These materials are often used in applications requiring high heat resistance or biocompatibility.
- Composites: Composite materials, which combine polymers with fibers like carbon or glass, offer enhanced strength and stiffness. These materials are used in FDM and other 3D printing processes to create lightweight, high-performance parts.
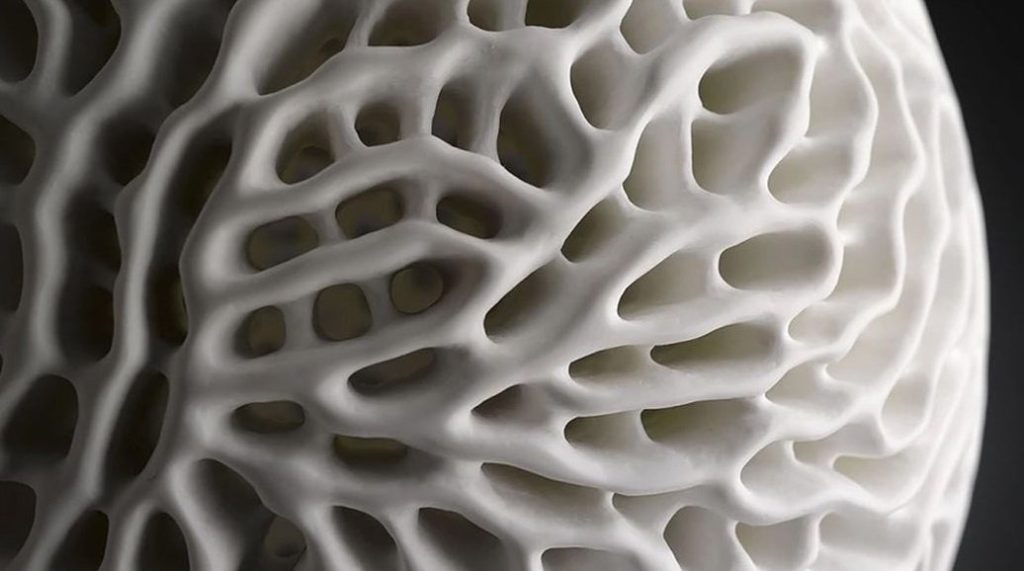
Applications of 3D Printing
3D printing has found applications across a wide range of industries, each benefiting from the technology’s unique capabilities:
- Prototyping: One of the most common uses of 3D printing is rapid prototyping. Designers and engineers can quickly produce prototypes to test form, fit, and function before moving to full-scale production. This accelerates the product development cycle and reduces costs.
- Healthcare: 3D printing is revolutionizing healthcare by enabling the creation of custom implants, prosthetics, and even bioprinted tissues. Surgeons can use patient-specific models to plan complex procedures, improving outcomes and reducing surgical risks.
- Aerospace and Automotive: The aerospace and automotive industries use 3D printing to produce lightweight, complex parts that improve performance and reduce fuel consumption. The ability to create parts on-demand also streamlines supply chains and reduces inventory costs.
- Education: 3D printing is increasingly being used in educational settings to teach students about design, engineering, and manufacturing. The hands-on experience helps students better understand abstract concepts and develop problem-solving skills.
- Art and Fashion: Artists and fashion designers are exploring 3D printing to create unique, custom pieces that push the boundaries of creativity. From intricate jewelry to avant-garde clothing, 3D printing offers new possibilities for artistic expression.
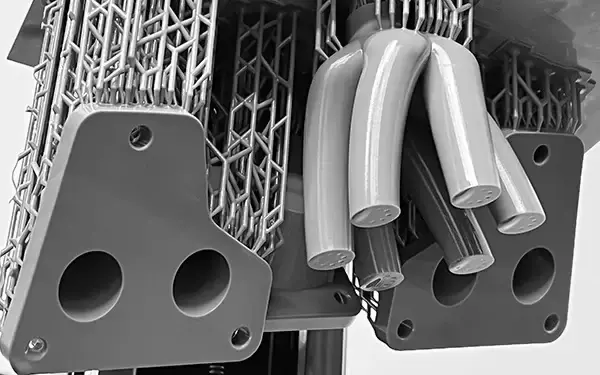
The Future of 3D Printing
The future of 3D printing is full of potential. As the technology continues to advance, we can expect to see even more innovative applications and materials. Researchers are working on developing faster, more efficient printers, as well as expanding the range of printable materials to include things like food and living tissues. In the coming years, 3D printing could become an integral part of everyday life, from personalized consumer products to large-scale manufacturing.
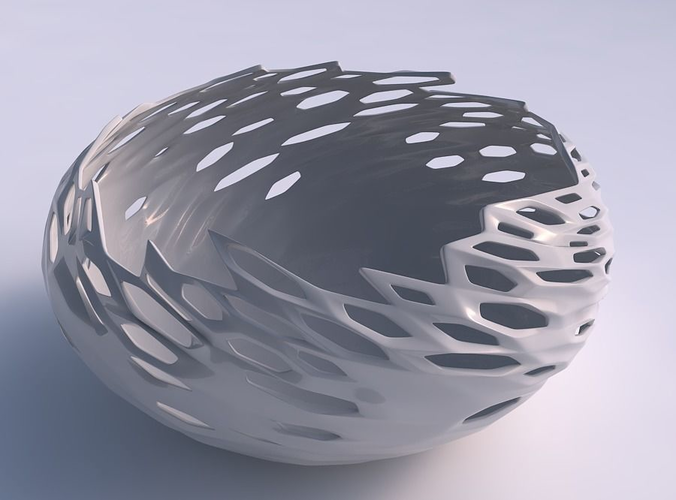
3D printing is a powerful technology that is changing the way we create and produce objects. Whether you’re a designer, engineer, or hobbyist, understanding how 3D printing works opens up a world of possibilities. With its ability to create complex, customized parts quickly and efficiently, 3D printing is poised to continue transforming industries and sparking innovation well into the future.