Around three decades ago, 3D printing emerged, unlocking a world of thrilling possibilities. Today, it’s possible to create everything from medical and dental prototypes to jewelry designs, miniatures, and even large-scale models in just a few hours. But who was the pioneer behind the first 3D printer?
When 3D printing made its debut about 30 years ago, it opened up a vast array of new possibilities. Today, we can produce medical devices, dental prosthetics, intricate jewelry, miniatures, and even large-scale models in just a matter of hours.
But have you ever wondered who invented the very first 3D printer? What was the initial 3D printing technique? And, perhaps most intriguingly, what was the first object ever created using 3D printing? The fascinating history behind 3D printing is full of surprising stories that might just astonish you!
Let’s take a journey back in time to discover how it all started:
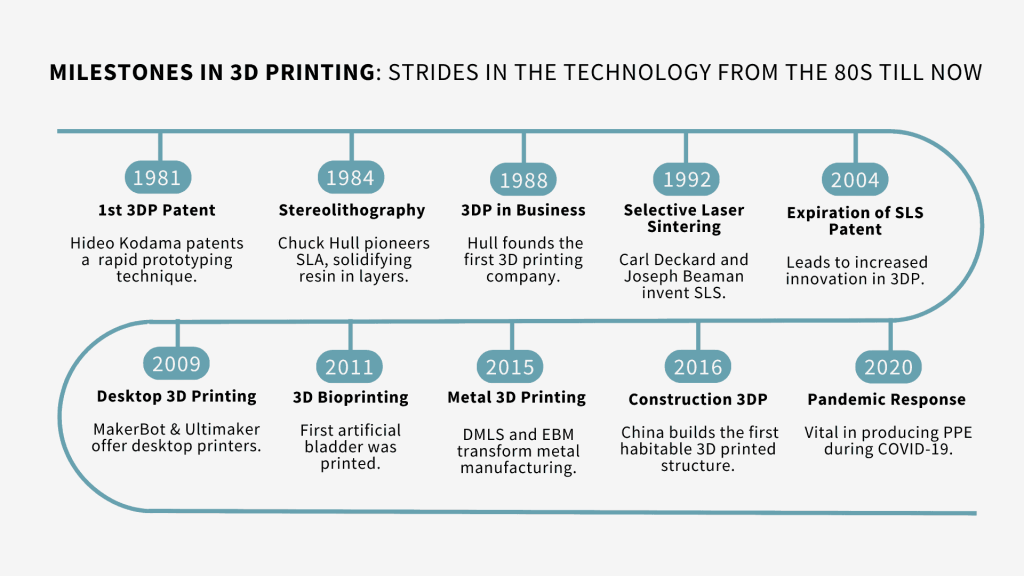
Phase 1: The Dawn of 3D Printing
Dr. Hideo Kodama and the Rapid Prototyping System (1980)
It may come as a surprise, but Dr. Hideo Kodama from Japan was actually the first person to explore 3D printing technology in the early 1980s. He was in search of a method to develop what we now call a rapid prototyping system, laying the groundwork for modern 3D printing.
Dr. Kodama devised a system that used UV light to solidify resin layer by layer, ultimately creating a tangible 3D model. Despite his innovative approach, Dr. Kodama was unable to fulfill all the necessary steps for patent approval, so his pioneering 3D printing technique never reached commercialization.
Chuck Hull and the Birth of SLA 3D Printing (1984)
While Dr. Hideo Kodama laid the groundwork, it was Chuck Hull who is often celebrated as one of the true pioneers of 3D printing. In 1984, Hull became the first to officially file a patent for what we now know as SLA (stereolithography) 3D printing. Hull coined the term “stereolithography” to describe the process in which layers of material are solidified using ultraviolet light to create a 3D object.
Hull didn’t stop there; in 1986, he founded his own company, 3D Systems, and in 1988, he introduced the first commercial 3D printer, the SLA-1. The SLA method requires resin, a light source, and digital files known as STL files to produce 3D objects.
Fun Fact: The very first item ever printed using a 3D printer was an eye wash cup!
Carl Deckard and the Advent of SLS 3D Printing (1987)
Around the same time as Chuck Hull’s advancements, another groundbreaking 3D printing technique emerged—Selective Laser Sintering (SLS). Unlike SLA, which uses resin, SLS 3D printing employs a laser to fuse loose powder into solid material.
Carl Deckard began developing the SLS method as an undergraduate student at the University of Texas at Austin. With guidance and support from his professor, Dr. Joe Beaman, Deckard continued refining this technique throughout his master’s and Ph.D. studies.
In 1987, Deckard and Beaman co-founded Desk Top Manufacturing (DTM) Corp. However, it wasn’t until 2006 that SLS 3D printing became commercially available. In 2001, their company was acquired by 3D Systems, the same company founded by Chuck Hull.
S. Scott Crump and the Invention of FDM 3D Printing (1988)
Interestingly, Fused Deposition Modeling (FDM) 3D printing was developed after both SLA and SLS techniques. In 1988, S. Scott Crump devised FDM 3D printing while trying to create a simple toy frog for his daughter. Using a hot glue gun and melted plastic, Crump layered the material to form the frog, sparking the idea for FDM technology.
Crump went on to patent this new technique and, in 1989, co-founded Stratasys with his wife, Lisa Crump. This innovation laid the foundation for one of the most accessible and widely-used 3D printing methods today.
Phase 2: The Path to Accessibility in 3D Printing
In the early days, 3D printers were bulky, costly, and not easily accessible to the general public. However, starting from the 1990s, 3D printing technology began to evolve rapidly. Companies, startups, scientists, and medical professionals started to experiment with these machines, leading to the development of diverse applications and innovative ideas.
One of the most groundbreaking advancements during this time was the emergence of bioprinting and other scientific applications, pushing the boundaries of what 3D printing could achieve.
Bioprinting Applications
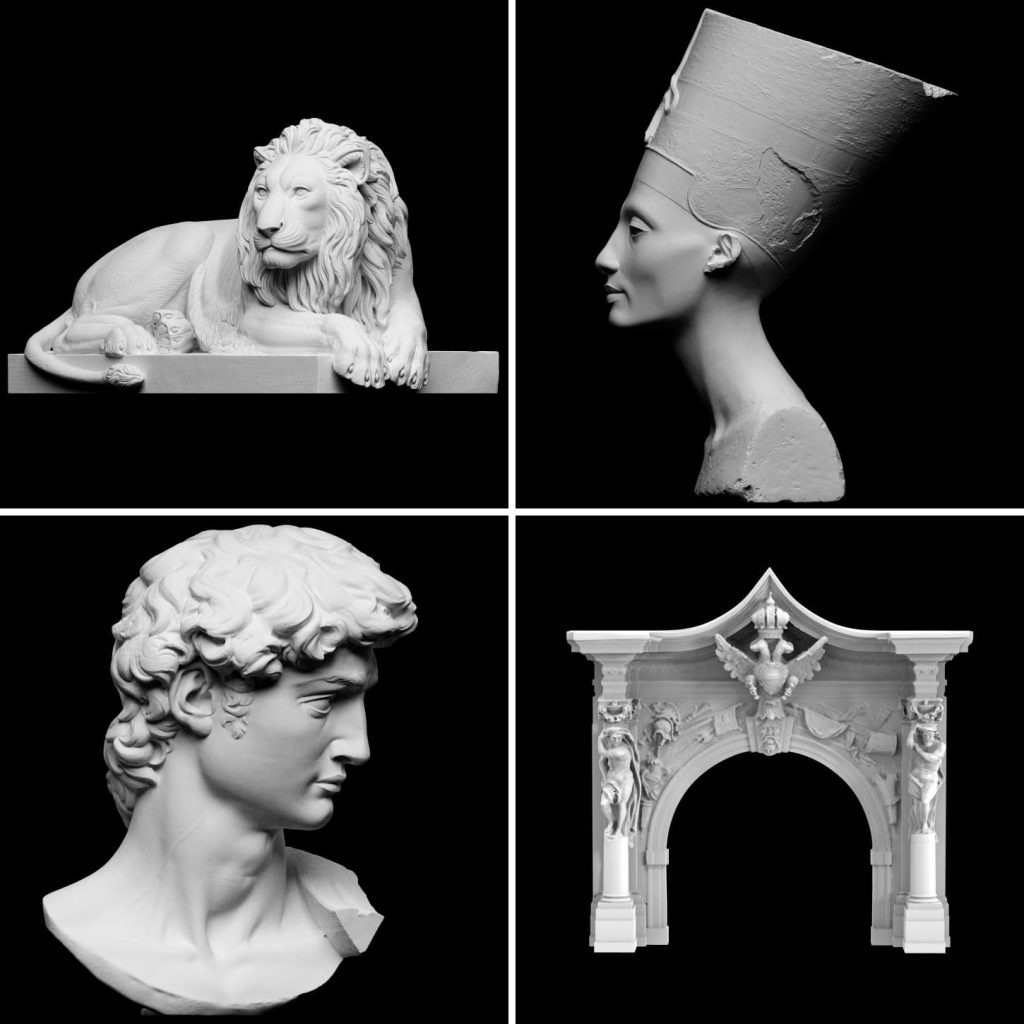
A scientific breakthrough occurred in 1999 when scientists built an artificial scaffold of a human bladder with a 3D printer. Human cells taken from a patient were then put into the scaffold which was used to grow a functioning bladder that was successfully transplanted into the same medical patient.
This then paved the way for a fully functional miniature kidney that was printed out by scientists in 2002. Using an animal model, the 3D-printed kidney could successfully filter blood and produce urine for the first time ever.
Since then, other organs such as a miniature liver, lung scaffold, and even a 3D-printed heart have all been created with the help of 3D printing. Using human cells and tissue, the first 3D-printed blood vessels were also produced during this time period.
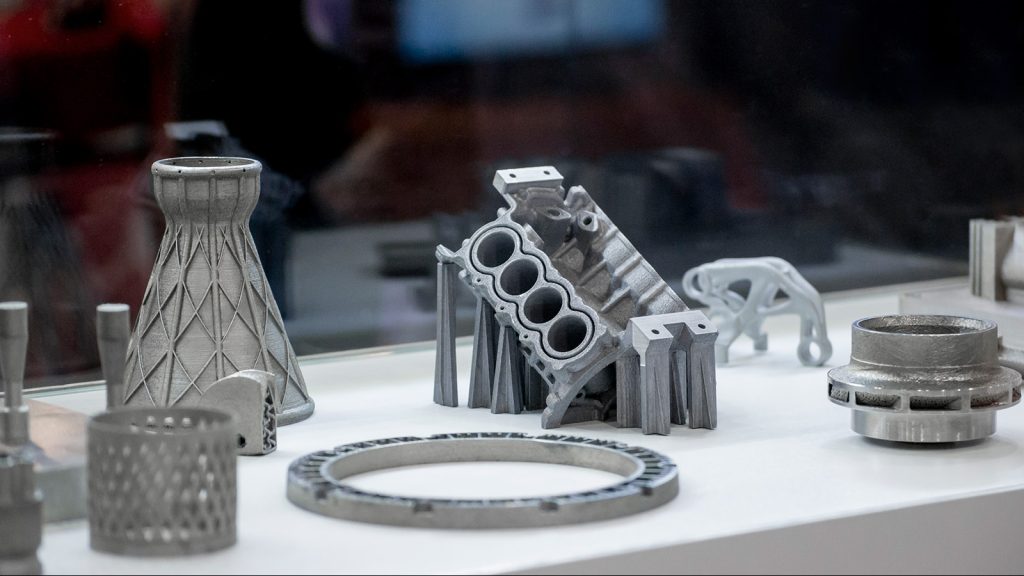
In 2008, a significant milestone in 3D printing occurred with the successful creation and implantation of the first 3D-printed prosthetic leg. This breakthrough allowed amputees to walk again and experience a renewed sense of wholeness.
Open Source 3D Printers
As 3D printing technology gained traction, the emergence of open-source 3D printers marked a pivotal development. These open-source resources democratized access to 3D printing, enabling enthusiasts, educators, and innovators to build, modify, and share their own 3D printers and designs. This movement accelerated the growth of the 3D printing community and fostered widespread experimentation and innovation.
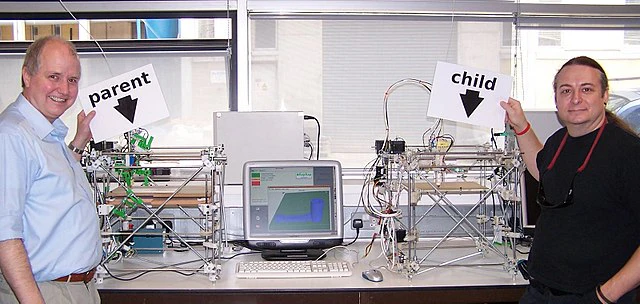
The evolution of 3D printing saw a transformative moment with the introduction of the RepRap project in 2005. Conceived by Dr. Adrian Bowyer from the University of Bath in the U.K., the RepRap project aimed to create a 3D printer capable of replicating its own components. This innovative approach was designed to make 3D printing more accessible, allowing users to print parts for others who did not own a 3D printer.
The RepRap initiative paved the way for the launch of Kickstarter, a crowdfunding platform where many 3D printing companies, including Phrozen, sought to gain visibility and support. Phrozen’s campaigns on Kickstarter, such as those for Phrozen Make in 2017 and Phrozen Transform in 2018, demonstrated their early adoption of 3D printing technology. Initially utilizing DLP 3D printing, Phrozen later upgraded to LCD technology, becoming a pioneer in Mono-LCD technology and significantly advancing LCD 3D printing.
Open-Source 3D Printing Files
With the rise of open-source platforms like Thingiverse, MyMiniFactory, and Cults, 3D printing files became widely accessible. These websites offer both free and paid 3D models, enabling users to share and download designs easily. The availability of 3D printing files has fostered a global community where anyone can access and print designs with their own 3D printers.
The development of user-friendly design software such as Tinkercad, Blender, and other CAD tools has further empowered individuals to create custom 3D prints. This software simplifies the process of designing unique and intricate 3D models, making advanced 3D printing accessible to a broader audience.
Phase 3: 3D Printing in the Present Day
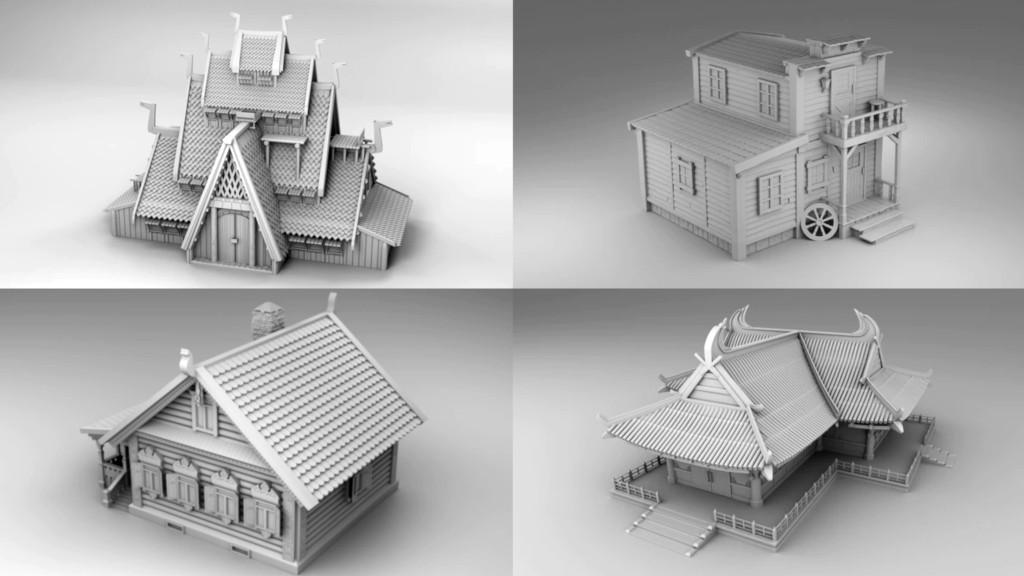
3D printers are incredibly popular today, thanks to their growing affordability and ease of use. Modern LCD 3D printers allow users to create highly detailed 3D models with exceptional accuracy and resolution. The accessibility of 3D printing has expanded significantly with the availability of 3D printable files, CAD software, and various resources for the general public.
Phrozen’s LCD 3D printers are versatile tools used across multiple fields, including jewelry design, dental applications, and hobbyist projects.
3D-Printed Jewelry
The advent of 3D printing has revolutionized jewelry design, enabling the creation of intricate and personalized pieces with remarkable precision. By using advanced 3D printing technologies, designers can experiment with complex geometries and custom designs that were previously challenging or impossible to achieve through traditional methods. This technology allows for rapid prototyping and customization, making it easier for both designers and customers to bring unique jewelry concepts to life.
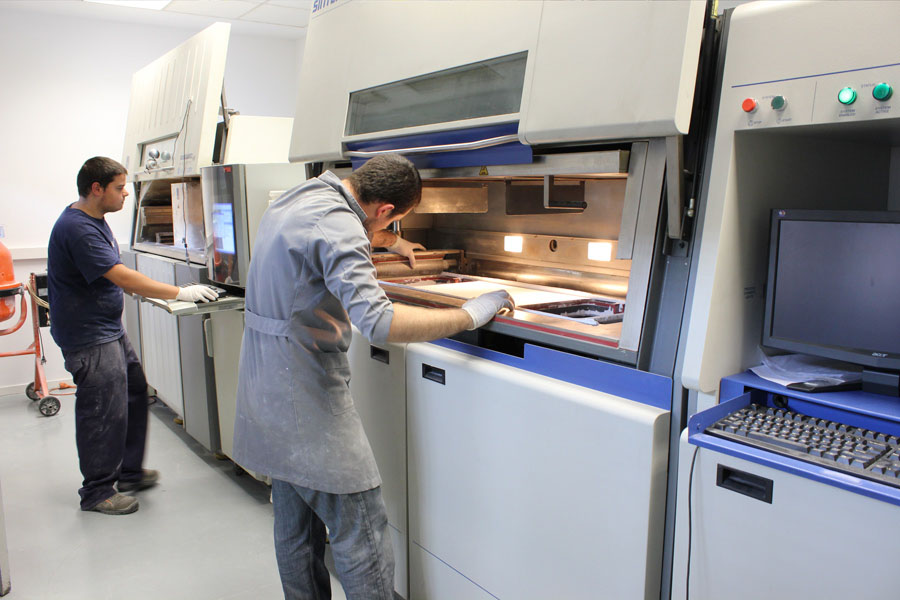
Jewelry 3D printing has transformed the industry by enabling the creation of highly intricate and precisely detailed designs. With this technology, custom accessories such as rings, bracelets, brooches, pendants, and more can be crafted with remarkable accuracy. This allows jewelry makers to refine and perfect their designs before committing to bulk production. For optimal results, consider using the Phrozen Sonic Mini 8K along with Wax-like Castable Resin.
Dental 3D Models
In the dental field, 3D printing is making significant strides by providing highly accurate and customizable dental models. This technology is used for creating everything from crowns and bridges to aligners and implants. By using 3D printing, dental professionals can produce precise models and prosthetics that fit perfectly, improving patient outcomes and streamlining the dental workflow.
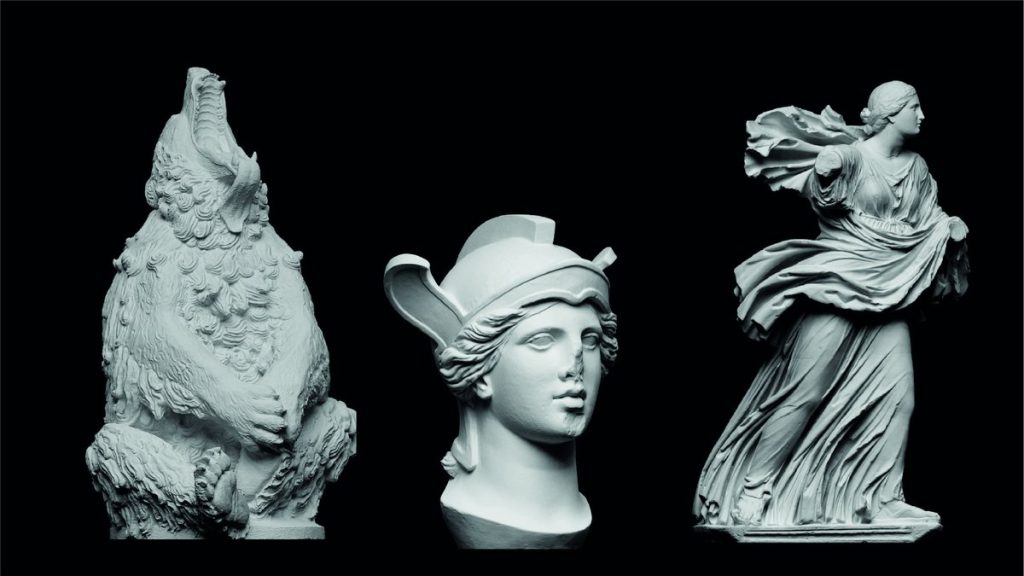
Boost your productivity with dental 3D printing. LCD 3D printers enable dentists to create detailed 3D dental models much faster than traditional methods, ensuring precise fits for dental parts and models. Phrozen LCD 3D printers, such as the Sonic 4K 2022 and Sonic XL 4K 2022, make it easy to produce professional-quality dental models, removable dies, immediate dentures, splints, and more.
3D Printing for Hobbyists
For hobbyists, 3D printing offers an exciting opportunity to bring imaginative projects to life. Whether you’re interested in crafting detailed miniatures, custom gadgets, or unique art pieces, 3D printing provides the tools to create virtually anything you can design. With advancements in technology, even enthusiasts with limited experience can produce high-quality, personalized items. From building intricate models to experimenting with new designs, 3D printing opens up endless possibilities for creative expression and innovation.
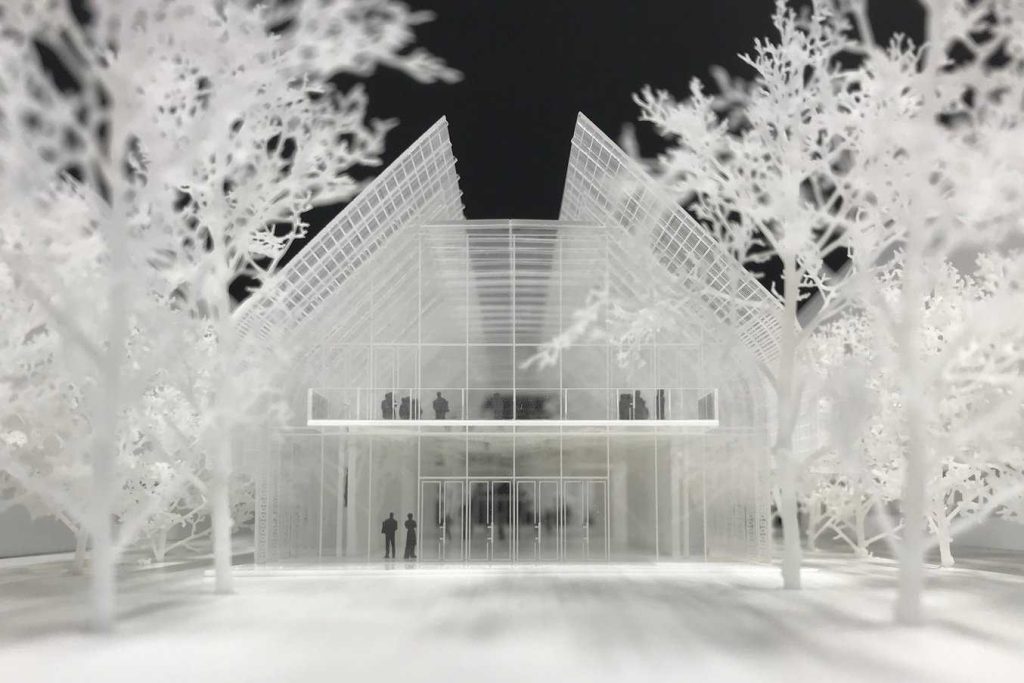
3D Model Credit: Bestiarum Miniatures
Resin printing offers hobbyists the chance to bring their favorite superheroes, anime characters, and more to life from the comfort of their own homes. Instead of buying action figures online, why not take on a 3D printing project and create your own unique models?
For large-scale 3D printing projects, the Sonic Mighty 4K or Sonic Mega 8K are excellent choices. If your focus is on highly detailed miniatures and intricate models, the Sonic Mini 8K is ideal.